Steering Knuckle
Steering knuckles contain wheel hubs or spindles, and attach to the suspension components of a vehicle. Made from nodular cast iron, forged steel and aluminium, the components are critical to front suspension safety, so quality surface finishes, precision radii and perfect machined flatness are required. Processing involves custom tools such as disc mills, drills and reamers.
YOUR MANUFACTURING CHALLENGES
- Drilling numerous holes with low cycle times, high quality and reliability.
- Creating a productive and reliable process for roughing the bearing bore and chamfer.
- Meeting productivity and quality requirements when finishing the tapered bore.
- Establishing an efficient and secure process for the finishing cut on the bearing location.
- Reducing cycle times for milling faces while maintaining quality and reliability.
- Maximising productivity when sawing locking nuts on the tie rod arm.
- Milling part faces with minimal setting and adjusting time.
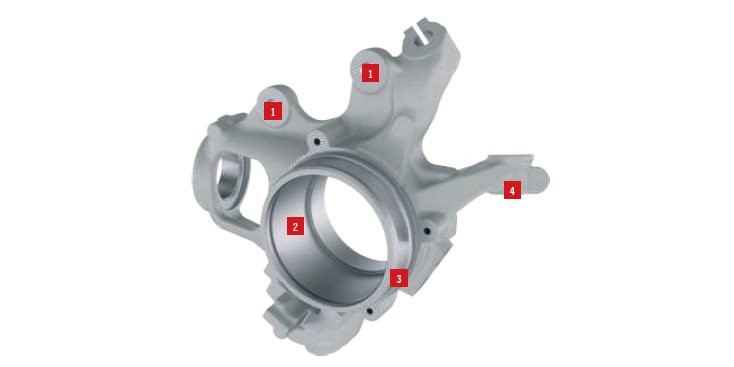
1 - Drilling numerous Holes
Your Challenge: | | Drilling numerous holes with low cycle times, high quality and reliability. |
Our Solution: | | Providing high performance when dealing with angled exits or intersecting holes, the Seco Feedmax Chamfer Drill utilises the light-cutting geometry and a special edge preparation to increase process security and tool life. The tool also incorporates a low-friction coating, and uses four land margins to increase stability. Your benefits include maintaining productivity in challenging, high-tolerance holes. |
Product: | | Seco FeedmaxTM Chamfer Drill |
| 2 - Roughing the bearing bore and chamfer |
Your Challenge: | | Creating a productive and reliable process for roughing the bearing bore and chamfer. |
Our Solution: | | Combining rough boring and chamfering operations, this custom tool enables high table feeds when using double-sided turning inserts with positive geometries. Through coolant holes optimize tool life and chip evacuation, while carbide anvils protect the seat pockets and ensure reliable operation. ISO/ANSI Duratomic® TK1501 inserts offer the highest metal removal rates. Your benefits include increasing the efficiency of your production with a highly stable process. |
Product: | | Step Boring Bar |
3 - Roughing and bearing bore and chamfer
Your Challenge: | | Creating a productive and reliable process for roughing the bearing bore and chamfer. |
Our Solution: | | This custom tool features an integrated HSK-A attachment to reduce weight and overhang, enabling it to be used with a high feed table. Positive geometry minimizes cutting forces and demands on the machine, and use of ISO/ANSI Duratomic® TK1501 inserts will maximize metal removal rates. Your benefits include boosting productivity and attaining optimal performance from your equipment. |
Product: | | OD Machining Tool |
4 - Finishing the tapered bore
Your Challenge: | | Meeting productivity and quality requirements when finishing the tapered bore. |
Our Solution: | | To allow for high table feed while maintaining accuracy, the Bifix reamer uses a coated blade and multiple guide pads to maintain stability. The coated blade provides long tool life and excellent surface finishes. Your benefits include highly productive precision machining with lower production costs. |
Product: | | BifixTM Tapered Reamer |
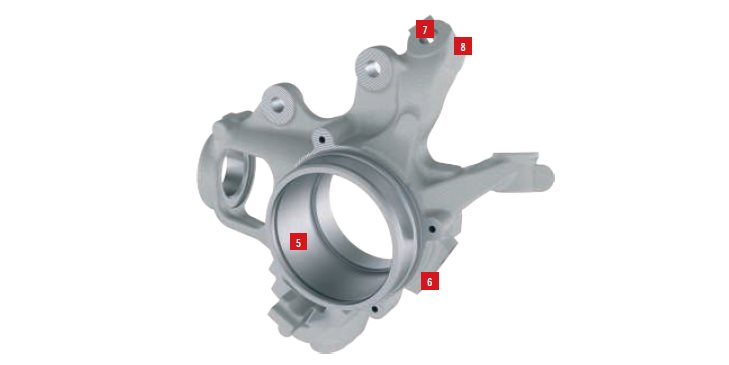
5 - Finishing cut on bearing location
Your Challenge: | | Establishing an efficient and secure process for the finishing cut on the bearing location. |
Our Solution: | | Maintaining high precision output while minimising cycle times, Xfix uses up to nine teeth to provide high feed rates, while holding tolerances as tight as IT6. Strong and stable insert cartridges ensure process security, while preloaded guide pads prevent vibration and increase stability. Your benefits include achieving tight tolerances without sacrificing the productivity of your production line. |
Product: | | XfixTM Multi-Tooth Reamer |
Your Challenge: | | Reducing cycle times for milling faces while maintaining quality and reliability. |
Our Solution: | | Turbo square shoulder mills use hardened steel cutter bodies and strong, thick inserts to achieve incredibly reliable performance and high material removal rates. These tools provide soft, easy cutting and minimize power consumption through their super positive cutting rake. Your benefits include increased confidence in your applications and substantial time savings. |
Product: | | Super Turbo Square Shoulder Milling Cutter |
| 7 - Maximising productivity |
Your Challenge: | | Maximising productivity when sawing locking nuts on the tie rod arm. |
Our Solution: | | Seco’s family of R335 disc milling cutters feature robust bodies for high tool life and incorporate a variety of features designed to optimize machining of cast iron. Positive rake angles reduce cutting forces and vibration to optimize accuracy and energy consumption, and the use of a constant rake angle over the radius maximizes chip evacuation. Your benefits include highly productive performance with extended tool life. |
Product: | | R335.19 Disc Milling Cutter |
Your Challenge: | | Milling part faces with minimal setting and adjusting time. |
Our Solution: | | Seco’s family of R335 disc milling cutters feature robust bodies for increased tool life and incorporate a variety of features designed to optimize machining of cast iron. Positive rake angles reduce cutting forces and vibration to optimize accuracy and energy consumption, and the use of a constant rake angle over the radius maximizes chip evacuation. Your benefits include highly productive performance with extended tool life. |
Product: | | R335.18 Disc Milling Cutter |