Cylinder Block
Cylinder blocks house the various main parts of an engine, such as liners and coolant passages. Block designs are often conceptually distinct and involve various different materials requiring bi-metal machining operations, as well as complex production processes and sophisticated high precision tooling.
YOUR MANUFACTURING CHALLENGES
- Eliminating vibration while productively milling both thrust faces.
- Maintaining productivity and reliability while square shoulder milling irregular stock, cast skin and impure surfaces.
- Maintaining productivity and reliability while face milling irregular stock, cast skin and impure surfaces.
- Achieving a secure and efficient process for roughing the crank bore line.
- Meeting high table feed and low cutting forces when roughing the cylinder bore.
- Meeting stringent tolerance and surface finish specifications when reaming.
- Establishing a productive process for milling small areas with irregular stock, cast skin and impure surfaces.
- Productively finishing main faces with high surface finish, flatness and waviness requirements.
- Drilling numerous holes with low cycle times, high quality and reliability.
- Reaming precise locating holes with perfect surface finishes.
- Minimising tool cost per piece when productively drilling numerous holes.
- Minimising cycle times when producing deep, high-quality holes.
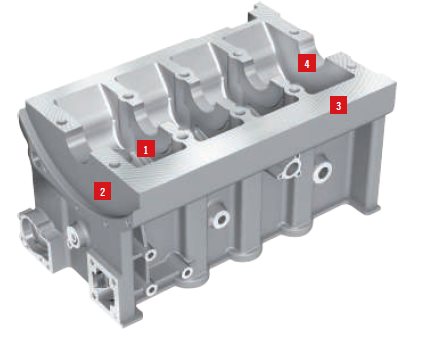
1 - Milling both thrust faces
Your Challenge: | | | Eliminating vibration while productively milling both thrust faces. |
Our Solution: | | | Seco’s family of R335 disc milling cutters contain robust bodies for high tool life and incorporate a variety of features designed to optimize machining of cast iron. Positive rake angles reduce cutting forces and vibration to optimize accuracy and energy consumption, and the use of a constant rake angle over the radius maximises chip evacuation. Additionally, the use of Steadyline vibration damping shell mill holders increases dynamic rigidity and allows R335 cutters to be applied with long overhangs. Your benefits include highly productive performance with extended tool life. |
Product: | | | R335.18 Disc Milling Cutter on Steadyline Arbor |
| | 2 - Square milling irregular stock, cast skin and impure surfaces |
Your Challenge: | | | Maintaining productivity and reliability while square shoulder milling irregular stock, cast skin and impure surfaces. |
Our Solution: | | | With a robust cutter body and thick, double-sided square insert, the family of R220.88 cutters provides aggressive material removal in cast iron roughing applications. This close pitch option was developed specifically for automotive components requiring productive milling of small surfaces. Your benefits include top performance and high productivity. |
Product: | | | R220.88 Square Shoulder Milling Cutter |
| | 3 - Face milling irregular stock, cast skin and impure surfaces |
Your Challenge: | | | Maintaining productivity and reliability while face milling irregular stock, cast skin and impure surfaces. |
Our Solution: | | | With sixteen cutting edges per indexable insert, Double Octomill significantly reduces the cost of obtaining high quality results. The tool provides superb surface finishes with maximum security, achieves tremendous cutter body life and can be used for both roughing and finishing. Your benefits include cost reduction while maintaining top performance. |
Product: | | | Double Octomill Face Milling Cutter |
4 - Roughing the crank bore line
Your Challenge: | | | Achieving a secure and efficient process for roughing the crank bore line. |
Our Solution: | | | Designed with strong tangential radius inserts, this custom tool offers extremely high rigidity for roughing the crank bore line. The center-lock insert clamping system ensures process stability while through coolant holes extend tool life and optimize chip evacuation. Your benefits include achieving constant stock removal on the finishing cut and improving tool life. |
Product: | | | Ball Nose Cutter |
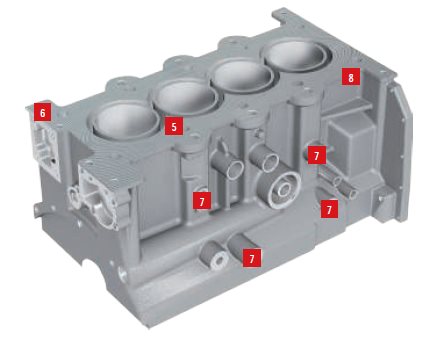
| | 5 - Roughing the cylinder bore |
Your Challenge: | | | Meeting high table feed and low cutting forces when roughing the cylinder bore. |
Our Solution: | | | This custom boring bar uses insert cartridges designed specifically to protect the tool body and allow fine adjustment to the positioning of CBN inserts, making it ideal for roughing operations. CBN 300 inserts with an E edge preparation should be used to reduce cutting forces. Your benefits include reliable machining when roughing cylinder bores. |
Product: | | | Boring Bar with CBN Insert |
Your Challenge: | | | Meeting stringent tolerance and surface finish specifications when reaming. | |
Our Solution: | | | For holes from 2.97 mm to 12 mm in diameter, Nanofix provides an ideal solution for achieving maximum precision. A multi-tooth solid carbide reamer with through coolant holes, Nanofix incorporates Quick-Fit tool changing, which eliminates the need to recheck overall length when replacing a reamer. Your benefits include easily obtaining high levels of precision in hole reaming. | |
Product: | | | NanofixTM Reamer | |
Your Challenge: | | | Establishing a productive process for milling small areas with irregular stock, cast skin and impure surfaces. |
Our Solution: | | | Specially designed for automotive applications requiring milling of small cast iron surfaces, the R220.38 super close pitch cutter reduces milling shocks. The tool offers a robust body and achieves maximum chip removal rates when used with tangential inserts. Your benefits include the ability to increase productivity by using more aggressive cutting data. |
Product: | | | R220.38 Super Close Pitch Cutter |
8 - Finishing main faces
Your Challenge: | | | Productively finishing main faces with high surface finish, flatness and waviness requirements. |
Our Solution: | | | Available in diameters ranging from 80 mm to 355 mm, the R220.30 offers superb finishing performance. Using a positive insert with four wiper cutting edges, the tool makes it easy to meet flatness and roughness requirements. MH1000 carbide grade inserts optimize performance for finishing operations in cylinder block face milling. Your benefits include an economical and easy-to-use tool for meeting your quality needs. |
Product: | | | R220.30 Face Milling Cutter |
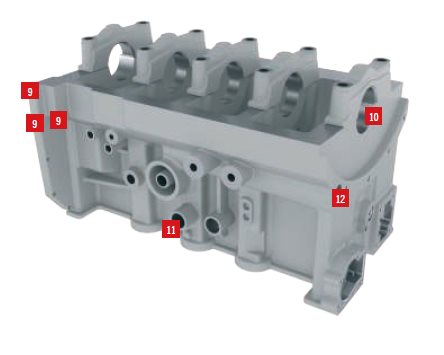
| 9 - Drilling numerous holes |
Your Challenge: | | | Drilling numerous holes with low cycle times, high quality and reliability. |
Our Solution: | | | Providing high performance when dealing with angled exits or intersecting holes, the Seco Feedmax Chamfer Drill utilises the light-cutting geometry and a special edge preparation to increase process security and tool life. The tool also incorporates a low-friction coating, and uses four land margins to increase stability. Your benefits include maintaining productivity in challenging, high-tolerance holes. |
Product: | | | Seco FeedmaxTM Chamfer Drill |
| | 11 - Reaming precise locating holes |
Your Challenge: | | | Reaming precise locating holes with perfect surface finishes. |
Our Solution: | | | An interchangeable head reamer, Precimaster™ Plus minimizes cost per hole while providing excellent results. Additionally, our Nanofix™, Precifix™ and Xfix™ lines fill out our range of reaming products, guaranteeing a productive and high quality solution for holes ranging from 2.97 mm to 155 mm in diameter. Your benefits include reducing costs while maintaining exacting tolerances and surface finish requirements. |
Product: | | | Seco Reaming Solutions |
| | 12 - Drilling numerous holes |
Your Challenge: | | | Minimising tool cost per piece when productively drilling numerous holes. |
Our Solution: | | | With strong indexable inserts and a highly stable, low-friction coated drill body, Perfomax achieves excellent productivity and economic performance. The drills feature optimized geometries to eliminate deflection and provide high chip evacuation. Your benefits include increasing throughput and minimising tool cost per part. |
Product: | | | Perfomax® Drill |
| 13 - Producing deep, high-quality holes |
Your Challenge: | | Minimising cycle times when producing deep, high-quality holes. |
Our Solution: | | Featuring sharp, positive and strong cutting edges that provide excellent hole quality, Seco Feedmax SD230A provides high performance in drilling holes of up to 30x tool diameter. Optimized geometries ensure process security, long tool life and exceptional performance in aluminium, reducing exit burrs and minimising workpiece deformation. Your benefits include reliable, productive and cost-efficient holemaking. |
Product: | | Seco FeedmaxTM SD230A |